今回の特集は「提案広がる労働安全」。労働災害はすべての現場で発生する可能性があり、ほんのわずかなきっかけが死亡事故や休業災害につながることもある。そこで本特集では実際の製造現場に焦点を当て、精肉加工を手がけるパルミート( […]
【自動車産業特集】ジェイテクト花園工場
工場長 辰巳 善紀氏に聞く サイクルタイム改善術
「元気な工場」の秘訣とは
挑戦と知恵のシナジー
工場には改善を楽しむ雰囲気が溢れていた。機械加工、手作業(歩行時間)も含め、ムダ・ムラ・ムリを見つけ出しサイクルタイムを縮め、ラインを圧縮し、生産性を上げる現場の担当者たち。機械加工では加工方法の変更、工具の変更はもちろん、機械停止時間、工具交換時間など少しでも改善の余地があれば手を加え、手作業も自動化できる要素があれば、からくり(ロー・コスト・オートメーション)を用いるなど徹底した改善を行う。サイクルタイムを短縮するために現場のみならず、製品設計も巻き込んで改善に結び付ける。同工場のテーマは「Yes,We Can!夢に向かって!!Be Ambitious!!(大志を抱け)」。1人1人の挑戦と知恵でコスト削減と効率化を図る。同時に挑戦しやすい環境を整え、「元気な工場」作りを推進する工場長の辰巳善紀氏に改善事例や現場を活性化させる秘訣を聞いた。
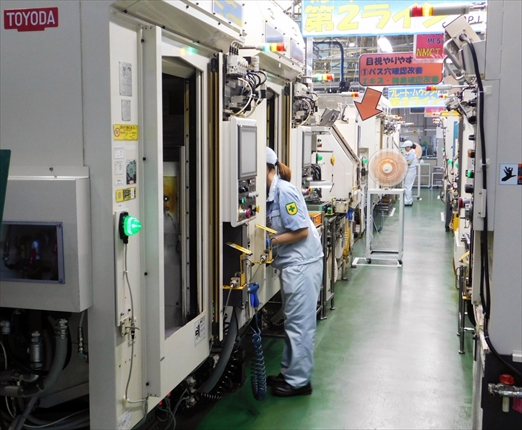
―現場の改善事例を教えてください。
第1工場はアルミ加工を主としており、旋盤、タッピングマシン、マシニングセンタ、手作業のラインがあります。サイクルタイムを縮めるため、機械加工や手作業の細かい要素を割り出し、『やめられないか、短く出来ないか』を合言葉に、自動化できる要素や改善可能な作業を見つけようとしています。改善事例は4WD車用電子制御カップリングの加工ラインのポンプハウジング加工やプレート加工でのサイクルタイムを89秒から50秒にした事例です。調べてみると、工程の中で刃具交換時間が全体の4割占めることが分かり、3つの改善を行いました。
―具体的には。
事例①は「刃具交換回数の削減」。例えば、異なる径のドリル加工やドリルとタップなど異なる加工を1つの工具に集約する工具のコンビネーション化を図り、加工項目の中で5つ共通化することで刃具交換時間を削減しました。そのほか、ワーク材種がアルミなので、切削工具を超硬チップから水素フリーDLCコーティングのチップにかえ、非常に薄膜なコーティングで切削性が良く、送り速度を上げ加工時間を4秒短縮し、工具寿命も4500回から3万回と長寿命化できました。
事例②は「主軸停止時間の短縮」です。改善前は主軸を停止すると惰性で回転し続け完全停止に3秒費やしていました。そこで回転指令を変更し、停止させるのではなく減速させることで、惰性で回転する時間が減り、完全停止する時間が1.2秒縮めることができました。
事例③は「刃具チェンジ時間の短縮」。従来の刃具チェンジは工具マガジン内の工具配置を右回りで右から加工位置に近い工具で0.5秒、一番遠い位置では2秒交換に時間がかかりました。改善後は右・左と両回りの工具交換に変え、より短い時間で工具交換を実現しています。
―細かい改善がなされていますね。そのほかに改善事例はありますか。
製品形状を変えて切削時間を短縮させた事例もあります。ポンププレート加工のミーリング加工は従来2回加工が必要でした。それを1回で加工出来ないか加工面の形状など検証したところ、カッター径が70㎜、プレート径が69㎜で2回加工している理由は1回で加工できない部分があり、お客様と相談し、加工できない部分は特に重要でない箇所だと確認できたので、図面を変更し1回の加工にすることができました。
そういった事例もあります。例えば、スプール油溝加工はスプール穴に油を逃がすため半円の加工をエンドミルで行いますが、ステップ加工であるためバリが出やすく、送り速度を上げられない欠点がありました。そこで油溝の必要性を調査して現場と設計が協力して新形状の設計にすることで加工しやすい穴の位置へ変更することができ、サイクルタイムを大きく改善できました。
―手作業現場ではどんなことを。
シグマCT(手作業+歩行時間)の大幅な削減を行うために様々な取り組みを行っていますが、特に手作業現場はなるべく効率の悪い作業をなくすために「からくり(ロー・コスト・オートメーション)」など装置を社内で作り活用しています。からくりは、てこの原理やカム、ギアなどを用いて、お金をかけず改善につなげる装置のことで、ワークを反転させる装置や冶具の出し入れ、ワークを持ち返る作業をなくすなど、メカニックな機構を利用しています。このような改善事例はお客様が訪問された際に、担当者が現場で事例紹介するなど改善活動を楽しんでいます。
―IoTや自動化について教えてください。
IoTの取り組みは現状行っていません。ラインの細かな情報はアンドンに上がる仕組みが出来上がっており活用しています。新規設備には自動化も取り入れていく予定ですが、すべてロボットありきではありません。手動ラインにロボットを入れると、安全面に懸念が残っているため慎重に検討していきたいと思います。
失敗おそれず積極的に
Yes,We Can.
―今後設備への取り組みは。
設備に関しては、第2工場でRP-EPSの生産ラインが立ち上がったため、RD-EPSのラインは徐々に縮小していきます。それは従来RD-EPSを供給していた車種もRP-EPSに置き換わっていくため、RD-EPSのラインを集約し、余った有休設備を第1工場へ移設活用します。第1工場は省スペース化や工程集約を図ります。市場的に油圧ポンプから電動ポンプに替わってきており、2つある油圧ポンプの生産ラインを段取り替えなどで1ラインに集約し、残った機械をオーバーホールや改造を加えて新しい生産品に適用させようと考えています。改善活動はラインの圧縮、工程短縮などにつながり、従来ラインを省スペース化し空いたスペースに新規案件を取り込んでいく予定です。
―多くの改善点を見つけ、実行する社内的な仕組みがあるのですか。
現場の困り事を第1と捉えています。毎朝各生産課のミーティングで品質管理、生産技術、工務関係の担当者が現場の困り事、やりにくい作業、安全対策など課題を出し合い、改善に向け話し合いをしています。管理職向け報告会も週1回設け、我々も活動をサポートしています。
―何か心掛けていることは。
「失敗しても良いから、積極的にチャレンジしよう」と日々言っています。何かしようとすると失敗は付いてくるものでしょう。それを恐れるのではなく、糧として次に活かせるようにしたい。社内でも『いけいけの辰巳』で有名です。
社内QCサークル改善事例発表大会で4年連続1位を取っています。社外でもQCサークル全国大会の愛知大会を優勝し東海支部大会に初めて進みました。工場のテーマは「Yes,We Can.be Ambitious to Dream!!(夢に向かって大志を抱け)」。現状維持だけでは活性化しません。改善活動だけでなく新しい仕事をどんどん取り入れ循環させることで「元気な工場」になっていけば、もっとみんながポジティブになれると思います。花園工場に来て今年で4年目になりますが、今後も「活性化」を目指すことを工場方針に据え進めていこうと思います。
―大変参考になる改善事例を紹介頂きました。長時間にわたりありがとうございました。
ジェイテクト花園工場 工場長
辰巳 善紀氏
1980年入社、豊橋工場の製造技術課や設備管理課などを経て、98年ステアリング事業本部海外事業管理部主担当、2000年海外勤務KSU(バージニア)出向、06年JATX(テキサス)出向など海外を担当、10年花園工場製造技術部部長、11年豊橋工場工場長、13年花園工場長、現在に至る。
日本産機新聞 平成29年(2017年)7月15日号
商品や提案の幅広がる/安全対策への投資意欲強く 「労働安全に関する需要は年々高まっている」。そう話すのはユアサ商事で、工具や安全対策商品を扱う機電本部の碓井利宏本部長。背景にはデジタル技術の革新による提案商材の拡大や、ユ […]
日本レヂボン「貼るだけでスリップ事故防止」 「ノンスリップテ—プ」は、階段や倉庫、製造現場の機械周辺の足場、浴槽周りの床などに貼りつけておくことで、床が滑りにくくなりスリップ転倒事故を防げる。テープを貼るだけの簡単な作業 […]